● レポート
ハーモWebセミナーレポート『高価な樹脂をムダにしない方法とは?』
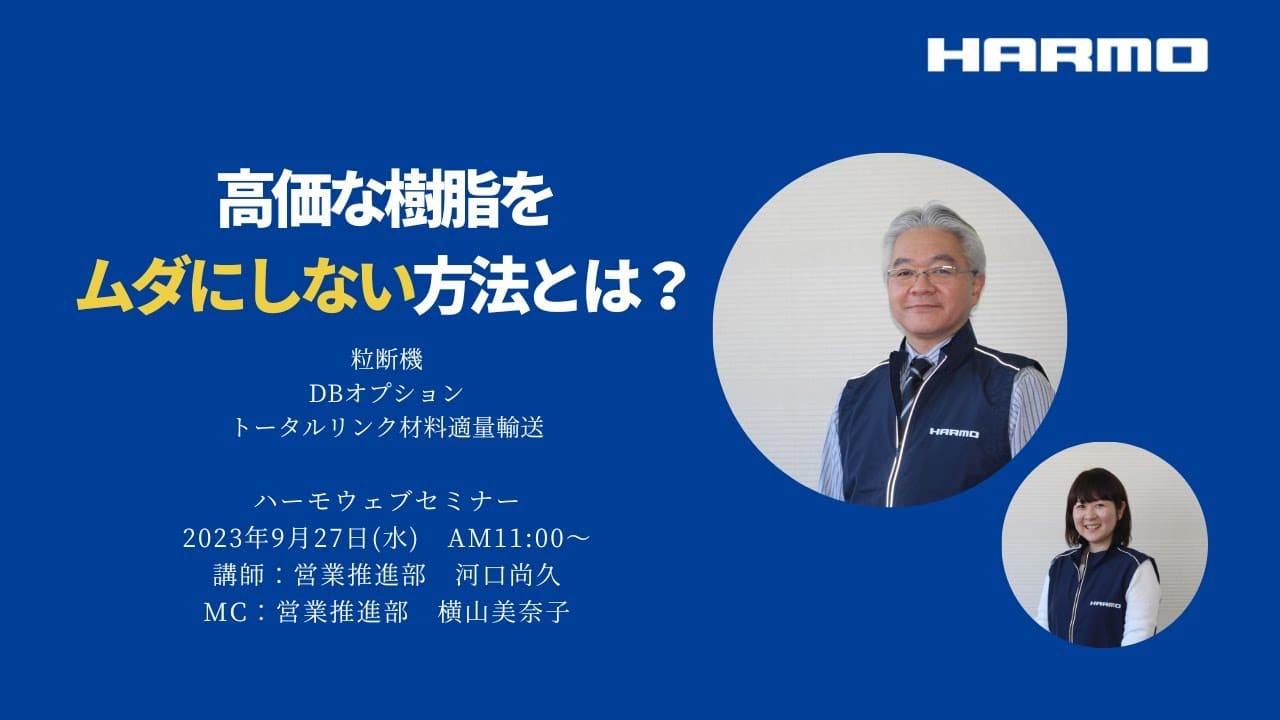
2023年9月27日に開催したハーモウェブセミナー【高価な樹脂をムダにしない方法とは?】の動画といただいたご質問への回答を掲載いたします。ぜひご覧ください。
ウェブセミナー資料をダウンロードできます
セミナーの資料をご用意いたしました。ダウンロードしてご活用ください。
ウェブセミナー内容
01. 高騰している樹脂原材料の現状について
合成樹脂の値上げ相次ぐ5〜8%、ナフサ上昇見込む
日本経済新聞9/19 より
- 石油化学メーカーが10月から汎用合成樹脂の価格を相次いで引き上げる
- 上げ幅は5〜8%とみられる。原料となるナフサ(粗製ガソリン)の価格上昇が見込まれるのを理由としている
- 自動車や電気製品の部材、包装資材といった価格の上昇圧力につながる
- プライムポリマーは10月1日納入分から、ポリエチレンとポリプロピレンの価格を1キログラムあたり15円以上引き上げる
- 旭化成はポリエチレン、サンアロマーはポリプロピレンをそれぞれ10月1日出荷分から1キログラムあたり20円以上値上げすると発表した
- 原油高や円安を受けて、国内で生産するナフサの価格上昇が見込まれているためだ。国産ナフサの価格は輸入ナフサの価格をもとに決める
- 輸入ナフサ価格の先行指標となるアジア地区のスポット(随時契約)価格は6月下旬に1トン500ドルを下回ったが、その後上昇基調に転じ、現在は700ドル台前半と3月上旬以来の高値水準にある
- 外国為替市場では円安・ドル高の流れが強まっている。日米の金利差を映した円安は輸入価格の高騰に拍車をかけ、国産ナフサ価格を押し上げる要因となる
- 石化メーカー各社は、10月に決まる7〜9月期の国産ナフサ価格を1キロリットルあたり6万2000円程度と予想している
- 4〜6月期に比べて1割近く安いが、2024年1月末に決まる23年10〜12月期は「(7〜9月期を大きく上回る)7万5000円程度を見込んでいる」(旭化成)という
02. ムダに捨てている樹脂の代表例
ムダに捨てている樹脂の代表例(1)
基本情報
樹脂名 | 成形品 | ㎏単価 | ランナ部質量 | 製品部質量 | サイクルタイム | |
PPS(GF40%) | 電子部品 | 2,000円 | 19g | 1g | 20秒 | 24時間成形 |
結果:ムダに捨てている樹脂は1ヶ月で4,924,800円
樹脂名 | 成形品 | ㎏単価 | ランナ部質量 | 製品部質量 |
24時間 | 4,320g | 8,640円 | 82,080g | 164,160円 |
1ヶ月 | 129.6㎏ | 259,200円 | 2462.4㎏ | 4,924,800円 |
ムダに捨てている樹脂の代表例(2)
基本情報
樹脂名 | 成形品 | ㎏単価 | ランナ部質量 | 製品部質量 | サイクルタイム | |
COP | レンズ | 4,000円 | 4g | 1g | 30秒 | 24時間成形 |
結果:ムダに捨てている樹脂は1ヶ月で1,382,400円
樹脂名 | 成形品 | ㎏単価 | ランナ部質量 | 製品部質量 |
24時間 | 2,880g | 11,520円 | 11,520g | 46,080円 |
1ヶ月 | 86.4㎏ | 345,600円 | 345.6㎏ | 1,382,400円 |
03. 高価な樹脂をムダにしないハーモの製品群
ハーモの「粒断機」なら粉砕機の課題を解決できます
高速粉砕機の課題
高速粉砕機は製品もスプル・ランナーも砕くことができる一方で、下記の課題があります。
- 粒が揃わず可塑化計量時間にばらつきが生じて、安定成形ができない
- 粉状の樹脂が多く、黒点・白点等の不良発生や、ホッパーローダーのフィルター掃除が頻繁に発生し、現場作業者の手間がかかる
- スクリーン(砕いた樹脂を分別する篩)をすり抜けた長い樹脂が、ホッパー内でブリッジを起こし、スクリューシリンダーへ樹脂が供給されず、成形機が止まり24時間成形ができない
低速粉砕機の課題
低速粉砕機では主にスプルランナーのリサイクルと併せて、機械トルクの許容範囲内での製品のリサイクルを行うことができる一方で、下記の課題があります。
- 粒度の均一性に難があり、粉状の樹脂も少なくありません
- 機械に使用される鋼材も高速粉砕機同様、一般にSKD材を使用しているため、ガラス繊維を含む樹脂のリサイクルでは機械構造が複雑であり、高速粉砕機以上にメンテナンスコストが発生するケースもあります
ハーモの粒断機ならそれらの課題を解決します.png?width=1280&height=670&name=%E3%83%8F%E3%83%BC%E3%83%A2%E8%A3%BD%E5%93%81%E3%82%B5%E3%82%A4%E3%83%88%7C%E7%B2%92%E6%96%AD%E6%A9%9FSPCIISPCIII%E3%82%B7%E3%83%AA%E3%83%BC%E3%82%BA%7Cogp%20(1).png)
ハーモの粒断機の特徴 ①
黒点・白点不良の原因とされる『粉状』の樹脂はほぼ出ません。
秘密はハーモ独自の「スイング・プレス・カット方式」
ハーモの粒断機は通常の粉砕機と違い、樹脂を一定のサイズで連続切断が可能です。粒も揃い、バージン材に近い形状のため、再生材による成形品質が安定します。詳細は下記の動画をご覧ください。
ハーモの粒断機の特徴 ②
独自の刃サイズで成形品の品質安定に貢献
プレスカットの一枚一枚のサイズ
- 小粒刃 2.1mm×3.5mm
- 標準刃2.8mm×4.5mm
刃のサイズがバージンペレットのサイズとほぼ同一なので、シリンダースクリューの供給ゾーンから圧縮・可塑化ゾーンへ樹脂を安定供給できます。
ハーモの粒断機の特徴 ③
バージンペレットとほぼ同サイズのリサイクル材を実現
ある企業様から、「粉砕材100%をもちいて成形した結果、他社と比べた品質安定性評価において最も安定した成形ができた」と評価いただきました。
再生材を乾燥しないで材料の無駄をなくす「ダイレクト・リターン・サイクロン・ブレンダー」
※ダイレクト・リターン・サイクロン・ブレンダー=DBオプション
DBオプションのメリット
粒断材の再加熱による強度低下を抑えられる(品質安定)
「再乾燥」による課題
- PPSやアクリル系透明樹脂などは、過乾燥による製品の色調変化や流動性の変化による品質異常を引き起こすと言った課題もあります。
- DBオプションは従来の粒断材を乾燥機へ戻す方法よりも再加熱が1回減るので、成形品の強度低下を抑えることが可能です。
- また、再乾燥の必要ないリサイクル材を更に乾燥することによる無駄な電力消費の低減にも繋がります。
混合材を乾燥機に戻した時の余剰材が少ない(ムダを省く)
- バージン材と粒断材を一定混合して乾燥機内にストックした場合、成形終了時に多くの混合材が残ってしまう場合が多いです。そしてそれは多くの場合廃棄されてしまいます。そこで、乾燥されたバージン材と必要量の粒断材を成形機に必要分だけ送ることで、材料のムダを減らすことができます。
- また、成形後除湿乾燥機内に残る余剰材はバージン材のみなので、成形後の余剰材の管理も容易です。
ヘリカルホッパーにより材料の分離を防げる(安定成形)
ヘリカルホッパーによる樹脂の均一供給
- バージン材とリサイクル材が成形機ホッパーへ供給
- ヘリカルホッパーで攪拌混合されてから、射出バレル内へ均一に供給
- 成形品の品質異常を防止
乾燥機の清掃時間が短縮できる
- 粒断材をMDRⅡへ入れると、粉だけでなく小粒も乾燥ホッパーに静電気で付着するため、バージン材のみの場合に比べ、清掃時間が3倍多く必要となる。粒断材を乾燥ホッパーへ入れないことが清掃時間短縮になります。
(当社比10分→3分)
材料輸送のホースが1本になる
材料輸送のホースが1本になり、配管が少ないので成形機回りがスッキリします。
材料輸送中の吸湿を防ぐクローズ輸送が標準
成形機ヘリカルホッパーへ材料を輸送する際に二次エアを外気から取り入れません。ブロアからの除湿エアをバージン材タンクに入れて輸送します。
成形直後の粒断材の含水率測定
コラボ機は粒断材を成形機へ直接戻します。その時に問題となるのは、粒断材の吸湿です。粒断材の時間経過ごとの含水率を水分量測定器で測定しました。
測定日 | 2020年1月9日 |
湿度/温度 | 23℃/10% |
材料 | PA6 |
乾燥温度 | 120℃ |
金型温度 | 85℃ |
MDRⅠで乾燥バージン材水分量 | 218PPM |
粒断直後の粒断材水分量 | 339PPM |
粒断1時間後の粒断材水分量 | 632PPM |
粒断2時間後の粒断材水分量 | 891PPM |
結果
ポリアミドの成形可能含水率は1,000PPMです。いずれの含水率も成形可能な数値となっています。(余裕をみて粒断後1時間以内に成形機へ再投入します)
DBオプションについての動画
トータルリンクで材料を適量輸送
樹脂材料換えの工程
成形品ごとの金型交換、それに伴い行なわれる段取り換え作業は「樹脂交換」「成形条件出し」「周辺機器の清掃や準備」など多岐に及びます。中でも、樹脂材料の交換は多くの手間と時間を必要とします。
多くの手間がかかる樹脂の交換作業
- 成形機上のホッパー内の樹脂を取り除く
- スクリューシリンダーへ洗浄剤を投入する
- バレル内の樹脂をパージして次の成形に備える
その上、次の成形を開始するまでには「金型温度調節機をセットする作業」「成形後の樹脂乾燥機の清掃」「粉砕機の清掃」など多くの作業を伴います。
さらに多品種少量生産やシングル段取り等の要求事項も多く、樹脂材料換え工程でやるべき事をやるべき時間内でできているのか、現状を正確に把握されている成形加工業者様は意外と少ないかもしれません。
必要以上にパージで捨てられる樹脂
成形終了後、成形機上のホッパーに残った樹脂の排出作業
- ホッパー下のシャッターを閉じる
- 樹脂排出口から余った材料を抜き取る
樹脂排出口が無い場合はホッパーのふたを外し、ホッパー内の残留樹脂を道具を使い取り出す作業を行なっているお客様も少なくありません。
これらの作業は手間と時間が掛かることから、ガラス管ホッパーに残っている樹脂をパージして捨てているお客様もお見かけします。特に、成形機の自動パージ機能は便利な機能ですが成形終了時に他の作業工程を優先してしまい、ホッパー内に樹脂が残ったままオートパージのボタンを押している作業者の方もおられるのではないでしょうか?
パージによる樹脂削減で見込める効果
成形機上のホッパーに樹脂が無くなると、ホッパーローダーは成形終了間近であっても自動的に一定量の樹脂を供給し続けます。
もし、成形終了にあわせて必要最小限の樹脂を供給ができれば、成形機上のホッパーから余った樹脂を取り除く作業や、ホッパー内に残った樹脂をパージして捨ててしまう無駄を省くことができ、「段取り時間の短縮」や「製造原価低減」の効果を実現できます。
また、パージによる廃棄樹脂の削減は、カーボンニュートラルスコープ3におけるCo2排出の削減効果にも繋がります。
Co2削減について詳細は下記をご覧ください
樹脂不足対策については下記をご覧ください
ハーモの取出ロボット機能でパージによる廃棄樹脂を自動削減
ハーモの『トータルリンク』は周辺機器の設定・起動・モニタを一括管理するRPA(Robotic Process Automation:ロボットによる業務自動化)システムです。
取出ロボットと連携することで、射出成形の自動化・品質向上・コスト低減を実現します。
廃棄樹脂を自動で削減する取出ロボットの機能
- 予め製品の生産数量を取出ロボットコントローラーへ入力
- 成形終了に併せて、成形機上へ供給する樹脂の輸送時間をロボットコントローラーが自動で演算
- 取出ロボットがホッパーローダーの輸送時間を制御し、成形終了時に必要最小限の樹脂を供給
トータルリンク 材料適量輸送
条件 | 現状 | 材料適量輸送 | ||
① | 1日の金型交換回数 | 2回 | ⇦ | |
② | 1回のパージ量 | 1,200g | 600g | 現状÷2 |
③ | 材料単価(/kg) | ¥1,800 | ⇦ | |
④ | 1ヵ月の稼働日数 | 20日 | ⇦ | |
⑤ | 1ヵ月のパージ回数 | 40回 | ⇦ | ①×④ |
⑥ | パージ樹脂量 | 48.0kg | 24.0kg | ②×⑤ |
⑦ | パージによる廃棄額 | ¥86,400 | ¥43,200 | ③×⑥ |
⑧ 1ヵ月で節約できる材料費 ¥43,200(現状-材料適量輸送)
⑨ 1年で節約できる材料費 ¥518,400(⑧×12)
導入台数が増えれば、節約できる材料費が更に増えます
- 1台 ¥518,400/年(⑨×1)
- 5台 ¥2,592,000/年(⑨×5)
- 10台 ¥5,184,000/年(⑨×10)
パージされた樹脂の廃棄料金を考えると、上記金額以上の効果になります。
事例
① 左の画像
- 連続生産中に何らかのエラーで成形機停止した
- 加熱筒とホッパー内の残量を廃棄した際の実例重量
- 夜中に取出ロボットが予定個数を終了して自然に材料が余ることと同等
② 右の画像
- トータルリンクによる材料調整機能を活用
- 材料ロス分をサンプルした実例平均材料
- PA6で成形した場合、平均1日614gが余り、①と比べると約半分で済む
ウェブセミナー資料をダウンロードできます
セミナーの資料をご用意いたしました。成形現場の課題解決にダウンロードしてご活用ください。
ウェブセミナーの動画をご覧いただけます