● レポート
ハーモWebセミナーレポート『射出成形における異物混入ゼロへ!原因から対策まで徹底解説』
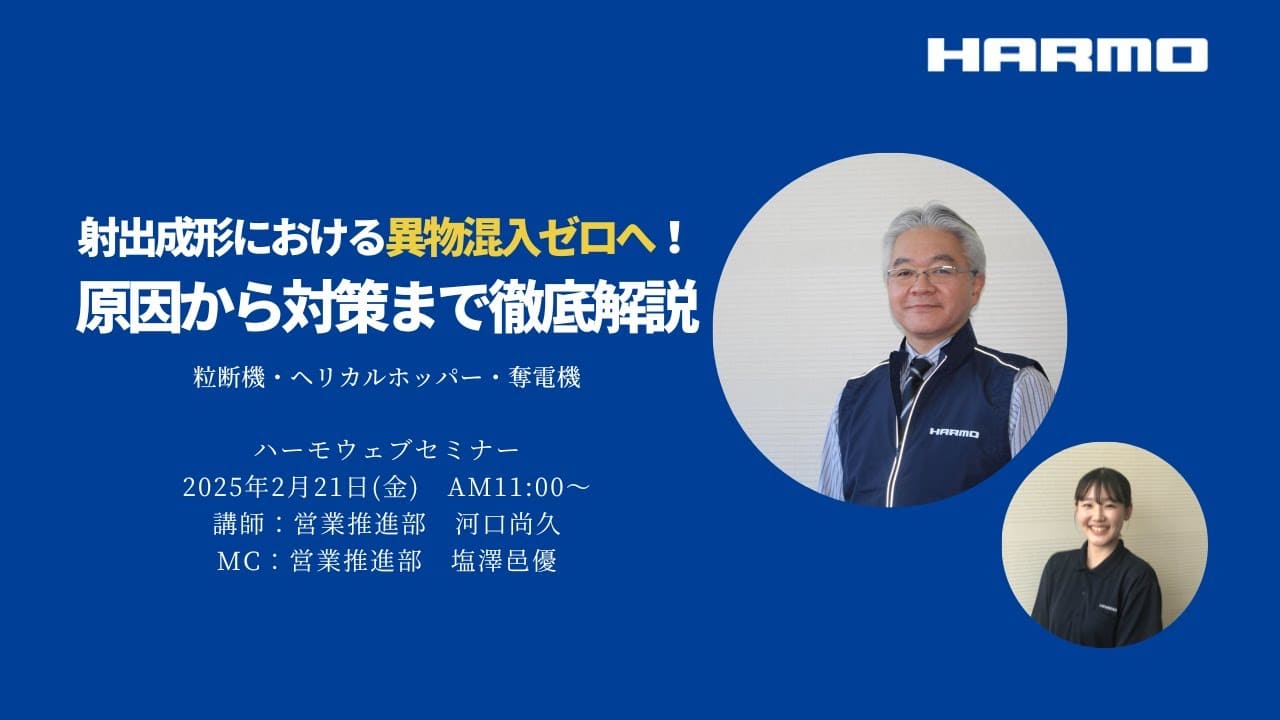
2025年2月21日に開催したハーモウェブセミナー『射出成形における異物混入ゼロへ!原因から対策まで徹底解説』の動画とセミナー内容を掲載いたします。異物混入の成形不良でお悩みの企業様はぜひご覧ください。
セミナー資料をご用意しました
セミナーの資料をご覧いただけます。ダウンロードしてご活用ください。
動画でもセミナーをご覧いただけます
ウェブセミナー内容
異物混入の発生メカニズムと主な原因
異物混入の発生原因
- 材料由来
- 環境由来
- 設備由来
- 作業者由来
1. 材料由来の異物混入
保管・輸送時
- 原料袋が破損し、ほこり、繊維が混入
- 輸送途中の樹脂同士の接触
再生材
- 粉砕工程で粉や微細なプラスチック片が混入
材料供給時
- 材料投入時に外部からほこりや異物が混入
2. 環境由来の異物混入
作業場の粉塵
- 作業場の汚れ・換気不良で粉塵が材料に付着
静電気
- プラスチック材料が静電気を帯び、ほこりや異物を引き寄せる
3. 設備由来の異物混入
金型・機械の汚れ
- 摩耗金型の摩耗やグリースが劣化し、異物が混入
機械内部の汚れ(ホッパー・乾燥機・スクリュー)
- 材料の炭化や焦げ付きが発生し、それが混入
4. 作業者由来の異物混入
作業管理の不備
- 手袋や作業着の繊維、工具の破片が混入
ヒューマンエラー
- 異なる材料の混入や、誤った材料の扱い
異物混入によるトラブルとその影響
異物混入が引き起こす4つのトラブル
- 外観不良
- 機能不良
- 強度低下
- 生産不良
1. 外観不良(見た目の問題によるクレーム)
主な発生原因
- 黒点異物の混入(炭化物・粉塵・金属片)
- 異種樹脂の混入(原料の取り違え・粉砕材の管理ミス)
- 静電気によるゴミ付着(粉塵・繊維くず・髪の毛)
影響
- 見た目の問題で不良品扱いになる(黒点・白点・くもりなど)
- 顧客クレームの原因となり、信頼が低下する
- 製品のブランドイメージが悪化する(特に食品・医療・高級品分野で致命的)
2. 機能不良(製品の性能低下・事故の原因)
主な発生原因
- 金属片の混入 → 通電不良・短絡(ショート)
- 異種樹脂の混入 → 材料の特性変化(接着不良・劣化)
- 油やグリースの混入 → 絶縁性の低下・機械部品の誤動作
影響
- 製品の性能が発揮できない(電子部品・医療部品で特に問題)
- 安全性に関わる重大なトラブル発生(部品破損・ショート・漏電)
- 製品リコールの可能性(企業にとって大きな損失)
3. 強度低下(材料の劣化による耐久性低下)
主な発生原因
- 炭化物の混入 → 成形品の脆化(強度低下)
- 粉砕材の劣化 → 分子構造が変化し、衝撃強度が低下
- 異種樹脂の混入 → 本来の特性が発揮できず、材料が弱くなる
影響
- 部品の強度が低下し、破損・クラックが発生
- 製品寿命が短くなり、早期故障の原因に
- 機械部品など重要なパーツに使用される場合、安全性リスクが高まる
4. 生産不良(製造工程への影響)
主な発生原因
- ノズル詰まり → 炭化物や異物が蓄積し、射出不良発生
- 金型へのダメージ → 金属片や異種材料の混入で金型が傷つく
- 粉砕材の粉塵混入 → スクリューの詰まり・成形不良の原因に
影響
- 成形不良の発生で生産性が低下(歩留まり悪化)
- 金型・スクリューが異物で傷つき、設備の寿命が短くなる
- 生産ラインが停止し、納期遅延のリスク増大
異物混入が引き起こす4つのトラブルと影響
- 外観不良 → クレーム・返品の原因
- 機能不良 → 安全性・性能低下のリスク
- 強度低下 → 製品寿命の短縮・破損の可能性
- 生産不良 → 設備ダメージ・納期遅延に繫がる
効果的な異物混入対策とは?
異物混入対策の3つの柱
- 発生源を減らす(粉の発生を抑制)
- 異物を確実に除去する(徹底的な異物排除)
- 静電気の影響をなくす(異物の付着を防ぐ)
1. 発生源を減らす(粉の発生を抑制)
ハーモの『粒断機』
再生材の問題点
- 粒が不揃いで、粉が多く発生
- 外観不良などの品質に影響
- バージン材でしか成形できず、リサイクル成形が難しい
「粉砕材」と「粒断材」
従来の粉砕機で処理した粉砕材は、細かい粉が多く見られ、また、細長い素材がそのままの大きさで排出されています。一方、粒断材の方は、粒も揃って、バージン材に近い形状をしています。粒状に切断するので、粉もほとんど発生しません。
その秘密はスイング・プレス・カット方式
スイング動作をする「プレス移動刃」と、本体に固定された「プレス固定刃」が噛み合うと、投入されたスプルやランナーが切断されると共に排出されるため、粉の発生する原因が少なく、熱や静電気の発生も最小限にとどめることができます。
回転刃で粗砕されたスプルやランナーは、プレス移動刃に対して直角に粒断され、一度カットされた材料は二度とカットされないため、粒の大きさが揃っています。細長いランナーがそのまま排出されるなどのミスカットや粉もほとんど発生しません。
ハーモの粒断機
飛散防止シャッター付きホッパーもご用意
粉砕中の破片や粉が飛び散るのを防ぎ、作業の安全や周りの環境を守ります。
『粒断機』導入のメリット
- 粉砕材による粉やカットミスを削減
- 再生材を使用した成形品質が安定
- 清掃・メンテナンスの手間を軽減
2. 異物を確実に除去する(徹底的な異物排除)
ハーモの『ヘリカルホッパー』
粉発生の原因と影響
- 輸送中に原料袋の中で樹脂同士が接触する
- 樹脂がホッパー等で輸送される時の樹脂同士の接触
- スクリューに付着した炭化物が材料に混ざり込む
ヘリカルホッパーの構造・原理
ヘリカルホッパー仕様(吸引式微分除去ホッパー)とは、エアにより回転分離動作と撹拌動作がホッパー内で行われ、樹脂原料表面に付着している微粉の除去を繰り返し行うホッパーです。成形不良の原因となる微粉を綺麗に除去し、成形品質を安定させます。
ヘリカルホッパーの構造・原理の動画
ヘリカルホッパーの粉取実演の動画
ヘリカルホッパーの内部スローモーション動画
『ヘリカルホッパー』導入のメリット
- 材料供給時の異物混入リスクを大幅低減
- クリーンな材料供給で製品の品質向上
- 簡単な設置で既存ラインに導入可能
3. 静電気の影響をなくす(異物の付着を防ぐ)
静電気による成形不良のお悩み
静電気によるコンタミ付着で、不良品の発生にお困りではありませんか?
- 成形品が静電気を帯びると中敷シートが反ってしまう
- 静電気反発により製品が崩れ、キズが発生する
- プラスチック射出成形品の表面には静電気を帯びる性質があり、静電気に引き寄せられて、空気中のほこりや異物が付着することがしばしば問題となります
- プラスチック射出成形における静電気は、金型のキャビティから離型する際に成形品表面とキャビティ表面が接触したり、摩擦によって帯電するパターンが多いようです
ハーモの『奪電機』送風いらずの瞬間除電!
奪電機の特長
これまでのイオナイザーの欠点
- 除電に時間がかかる
- 送風機がうるさく、ホコリが風で舞う
- オゾンくさい(有害)
- 除電後にイオンが離れて再帯電することがある
奪電機の特長
- 高速物体でも瞬間的に除電できる
- 物体がプラス、マイナスのどちらに帯電していても対応
- オゾンが少ない(通過時のみ)
- 原理的に再帯電しない
奪電機の効果を最大限発揮するための設置方法
使用例1
取出ロボットに奪電機を取り付けることで、二次降下時に奪電し、後工程での静電気影響を防ぎます。
使用例2
奪電機を金型下に配置する事で、成形品を落下回収する際に奪電し、後工程での静電気影響を防ぎます。
使用例3
コンベア出口に奪電機を配置する事で、製品の箱詰め前に奪電し、後工程での静電気影響を防ぎます。
『奪電機』導入のメリット
- 静電気による異物の付着を防ぎ、品質安定
- 黒点や繊維くずの付着を減らし、仕上がり向上
- 送風機の騒音やホコリの舞い上がりを抑える
実際に異物混入を減らせた成功例
ヘリカルホッパー 導入事例
- 半導体工程における粉の問題で困っていた
- 半導体製造のためのガラス基板のケースが粉による成形不良を起こしていた場合、アウトガスが発生。ガラス基板そのものにもそれが転移してしまい、ウエハに転写する際のレーザー電光を曇らせてしまう
- ケースの成形製造の前の樹脂材料の段階から粉をほぼ完全に除去して、成形後のアウトガスを発生させないようにする
ヘリカルホッパーで検証
検証方法
- 目的:ペレットに任意の微粉を混ぜ、ヘリカルホッパーの異物除去効果を確認する
- 材料:導電性樹脂(ペレット)
- 微粉:上記ペレットの材料袋内部にある微粉を使用
- 方法:ヘリカルホッパーで「ペレット単体」、「ペレット+微粉」の通過後を確認
ヘリカルホッパー通過後の各条件のペレットの状態
検証結果
他社と比べて樹脂材料に混ざった粉が取り切れているとの評価となり、ハーモのヘリカルホッパーが採用となった。
奪電機 導入事例(コネクタメーカー様)
奪電機の導入前は成形品が静電気で飛び散り、扱いに苦慮されていました。
奪電機の設置方法
奪電機の効果
動画でもセミナーをご覧いただけます
資料をダウンロードしてご活用ください