知っておきたい取出ロボットの最新活用事例
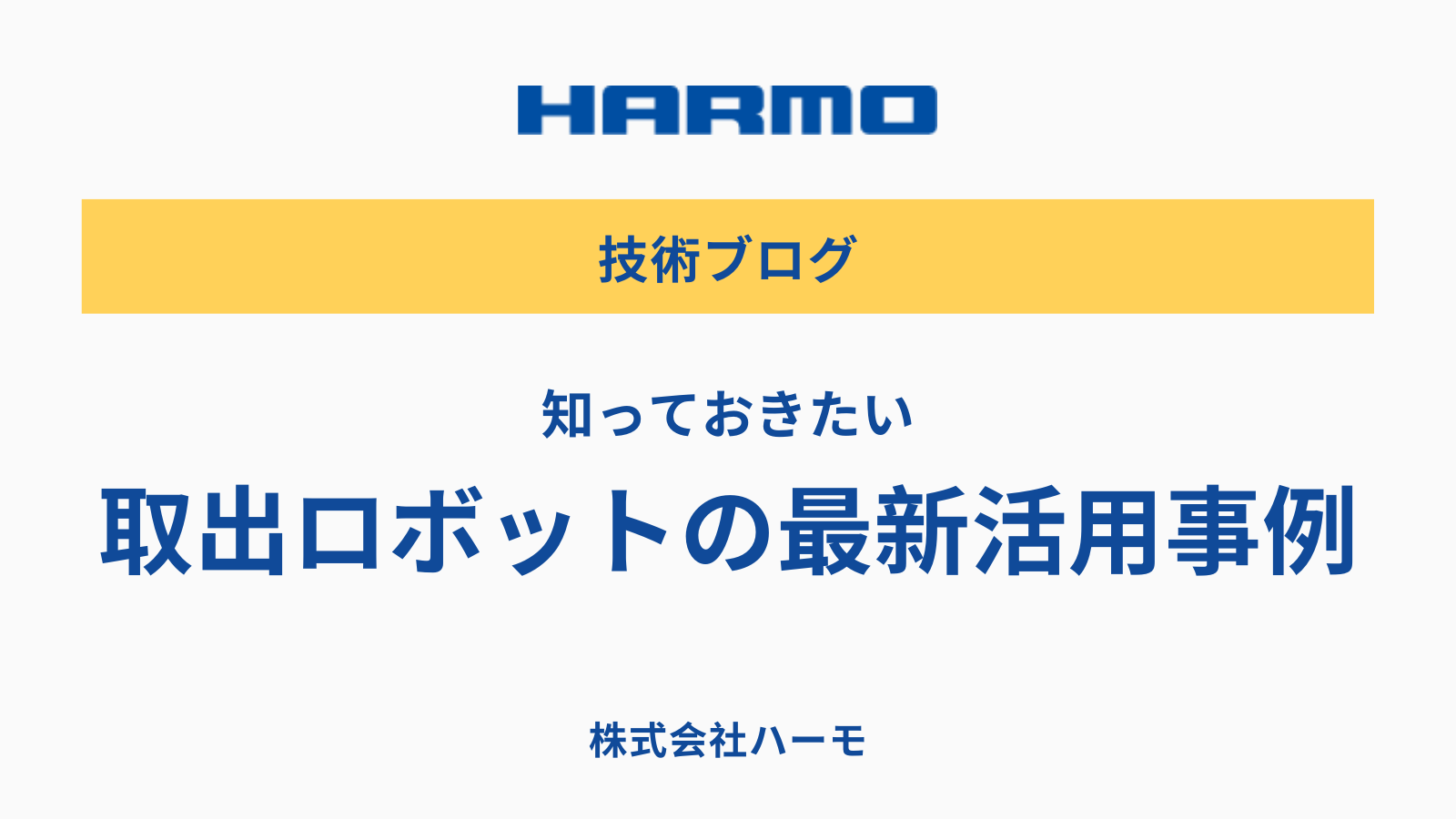
取出ロボットに求められること
射出成形で使用される取出ロボットの役割
- 金型から製品を取り出す
- 自動でゲートカットする
- コンベアやストッカーへ成形品を整列させる
- 二次加工機やカメラ検査機と連動する
- インサート成形においてはインサートワークを金型へインサートする
主に省人化・自動化を目的として使用されます。そこに求められる取出ロボットの機能は「速度」「停止精度」「操作性」「プログラムの自在性」などが挙げられます。
成形現場で抱える課題
成形現場で抱える課題は「成形機稼働率の向上」「ヒューマンエラー防止」「品質異常の早期検知」「材料ロスの低減」など多岐に及びます。
成形機稼働率の向上
成形機稼働率を上げられない理由としては「金型交換」「周辺機器の段取り替え」「成形条件の変更」などに多くの時間を要するため、成形終了から次の成形を開始するまでの時間を短縮できず、成形機稼働率を上げられない課題があります。
ヒューマンエラー&品質以上
ヒューマンエラーや品質異常を早期検知できない理由としては「人員確保難から一人当たりが受け持つ成形機台数が増加する」「作業員の高齢化」「作業員の熟練度不足」などを背景に、周辺機器の設定ミス、周辺機器の起動忘れ、成形品の抜き取り検査の不備、周辺機器異常による品質異常の発見が困難などの課題があります。
材料ロスの低減
材料ロスを低減できない理由としては、段取り替えを急ぐあまりに、成形終了時の余剰材料を成形機上のホッパーから抜き取らず、パージを続けて廃棄してしまうケースもあり、製造原価を低減できない課題があります。
新たな取出ロボットの活用方法
成形現場で抱える課題は取出しロボットの新たな機能の活用で解決することができます。ハーモの取出ロボットは求められる速度・停止精度・操作性・プログラムの自在性に加えて、周辺機器との連動機能・監視機能を備えており、成形現場の様々な課題を解決することができます。
ハーモのトータルリンク
射出成形の生産ラインをまるっと管理
ハーモのトータルリンクで周辺機器の設定・起動・モニタを一括管理し、射出成形の自動化・品質向上・コスト低減を実現します。
導入事例1. 段取り時間短縮の課題を抱えていたA社様
A社様の特徴
下記のようにA社様では比較的多くの成形機を担当していました。
- 型締め力150トンクラスの射出成形機を32台保有
- 現場作業者一人当たり受け持つ成形機台数は8台
成形機の段取り作業
一般に150トンクラスの成形機では下記の段取り作業が発生します。
- 金型交換に関わる段取り作業
- 材料交換に関わる段取り作業
- 各機器の条件設定や調整に関わる段取り時間
現場作業員の課題
上記作業に1~2時間掛かり、現場作業員の方が一人で多くの成形機受け持つため下記のような課題が生まれます。
- 段取り時間を短縮できず生産性が上がらない
- 成形終了のタイミングが重なる成形機では、段取り替え作業が重複するため、成形機の停止時間が長くなり成形機稼働率を上げられない
トータルリンクの導入で生産性を向上
段取り時間短縮を目的にトータルリンクを導入いただいたところ、金型交換作業に伴う周辺機器の段取り時間を成形機1台当たり24分短縮し生産性が向上しました。また、成形終了のタイミングが重なる成形機の停止時間の短縮により、成形機稼働率も向上しました。
導入事例2. 周辺機器の再起動を忘れ、多くの不良品を出してしまったB社様
停電による再起動の失念で多くの不良品が
B社様では夏場に多い落雷による停電で周辺機器の電源を喪失、ヒューマンエラーにより金型温度調節器の再起動を忘れてしまい、3時間後に品質異常に気付き、多くの不良品を出してしまいました。
停電後の再起動の際、成形機や取出ロボットは作動しているか目視で確認が可能です。一方、金型温度調節器や材料乾燥機は作動しているか目視での確認は難しく、再起動忘れのヒューマンエラーに課題を持っておられました。
パトライトを取り付けて対応されていましたが、比較的狭い機械間隔に置かれた周辺機器は多数存在し、パトライトの警告を見落とすケースもありました。
トータルリンクの導入でヒューマンエラーを解決
ヒューマンエラーの低減を目的にトータルリンクを導入したところ、停電復帰後ロボットの再稼働と同時に各種周辺機器も自動で再稼働でき、ヒューマンエラーによる品質異常は無くなり、再復帰に伴う段取り時間の短縮も実現されました。
導入事例3. 周辺機器の異常に気付かず、多くの不良品を出してしまったC社
様成形中の周辺機器の異常は作業者によって発見することは難しく、多くのお客様では「周辺機器が稼働しているか/稼働していないか」をパトライトで確認されています。
パトライトで発見できない異常
- 金型温度調節器からの媒体流量に異常がある
- 金型温度調節器の温度に異常がある
- 除湿乾燥機の温度に異常がある
上記の異常はパトライトでは確認できません。そのため、作業者により不良品を発見するまで、不良品を長時間生産してしまうリスクがあります。
C社様の課題
- 早期に品質異常を確認できず多くの不良を出してしまった
- 品質異常は何に起因していたか、トレースできない
トータルリンクの導入で品質異常の早期発見
トータルリンクでは「成形自動運転中の周辺機器の温度」や「金型温度調節器の媒体流量をロボットコントローラーが監視します。温度や流量の異常を検知すると、ロボットは自動で不良品かもしれない成形品を別の場所へ選別します。
作業者は不良品かもしれない製品を確認し、異常無ければ自動運転を続行でき、異常の際は選別された不良品を排除して、不良品の流出を防止することができます。
また、ロボットコントローラーは周辺機器の異常タイミングを記憶でき、不良の原因をトレースできることで、品質異常の早期発見と原因追及を可能にしました。
導入事例4. 原価低減とCo2削減に課題を持たれていたD社様
成形終了と共に行う材料替えは射出塔の中の樹脂を排出させる作業を伴います。成形機上のミニホッパーに残る樹脂は全て排出してから樹脂パージを行い、洗浄剤を投入してスクリューシリンダーの洗浄を行います。
D社様の課題
課題1
D社様では段取り時間短縮の取り組みを強化するあまり、現場作業者が成形機上のホッパーから完全に余剰材を排出せず、成形機のオートパージ機能を使用し、余剰材の多くをパージして廃棄してしまい、材料原価低減に課題を持たれていました。
課題2
また、D社様では、脱炭素にも取組まれており、無駄な樹脂使用の削減によるスコープ3のCO2削減対応の課題も持たれていました。パージされた余剰材は外部の廃棄業者により引き取られ、埋設か焼却処理を行います。焼却の際はCO2の排出を伴います。また、樹脂原料を生産する際にもCO2排出を伴うため、廃棄樹脂の削減はCo2削減に繋がります。
トータルリンクの導入で品質異常の早期発見
トータルリンクでは成形終了に併せロボットコントローラがホッパーローダーの材料輸送時間を最適にコントロール。必要最小限の樹脂をホッパーへ輸送します。
よって、成形終了時のパージによる廃棄樹脂を最小限にとどめ、余剰材の廃棄量削減による原価低減とCo2の削減を実現されました。