● レポート
ハーモウェブセミナーレポート『射出成形のおける「粉」の本当の問題点とは』
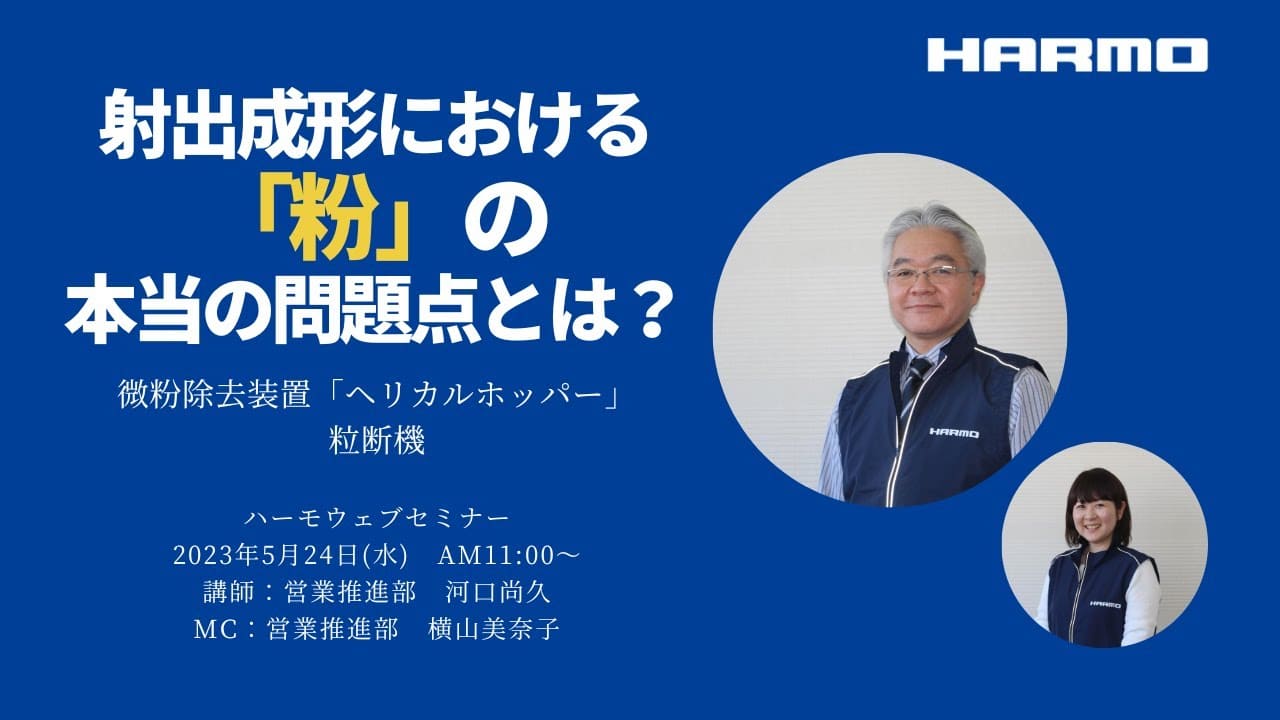
2023年5月24日(水)に開催したハーモウェブセミナー『射出成形のおける「粉」の本当の問題点とは』の動画といただいたご質問への回答を掲載いたします。ぜひご覧ください。
ウェブセミナー資料をダウンロードできます
セミナーの資料をご用意いたしました。ダウンロードしてご活用ください。
ウェブセミナー内容
- 成形不良で一番多い原因とは?(2:10~)
- 射出成形機メーカーに聞いてみた!粉の問題点とは(8:52~)
- 実際にお客様で起きた粉による問題点(11:59~)
- 徹底的に粉塵を除去する「ヘリカルホッパー」の紹介(16:47~)
- ヘリカルホッパー導入事例の紹介(21:25~)
- 再生材による成形品質安定に貢献「粒断機」のご紹介(25:55~)
01. 成形不良で一番多い原因とは?
成形不良の種類とその原因
成形品表面の欠陥による成形不良
★印 周辺機器で解決できる成形不良
シルバーストリーク(銀条) ★
成形面の表面に銀白色のすじが発生する成形不良
【想定される原因】 樹脂(ペレット)の予備乾燥不足
ひけ
成形品の表面の一部がへこむ成形不良
【想定される原因】 金型密着表面の冷却の遅れ
ショートショット(充填不足) ★
成形品の一部が欠ける成形不良
【想定される原因】 成形機の能力不足、材料の流動性不足、ゲート断面積が小さい、成形品肉厚が薄い、ガス逃げ不良など、溶融温度・金型温度が低い
ウエルドライン(ウエルドマーク) ★
金型内で溶融樹脂が合流した箇所に線状跡が発生する成形不良
【想定される原因】 樹脂の溶融温度が低い、金型温度が低い、孔箇所が多い、樹脂の流動性不足(位置の調整)
焼け、黒条
成形面に黒い変色や黒いすじが発生する成形不良
【想定される原因】 射出圧力が強すぎる、成形温度が高すぎる、金型内の空気抜け不足
黒点・白点/色むら・くもり ★
成形品に黒い点、透明成形品の白い点/有色成形品の色のくもりやむら
【想定される原因】 再生材もしくは、輸送途中に発生する材料中の粉が原因/ガス、予備乾燥不足
ジェッティング
成形面のゲート箇所から蛇行した縞模様が発生する成形不良
【想定される原因】 ゲートのサイズや位置、射出速度
フローマーク
成形面の表面にゲートを中心とした波状の模様が発生する成形不良
【想定される原因】 樹脂の溶融温度、金型の温度が低い、射出圧力が低い、射出速度が遅い
すり傷
成形品の側面などにこすれた跡がでる成形不良
【想定される原因】 抜き勾配の不足、成形品の投出時の傾きなど
成形品の割れによる不良
割れ・クラック ★
成形品の一部が割れたり、ひびが入ったりする不良
【想定される原因】 材料の水分残りを要因とする加水分解による強度不足
白化
成形品の突出ピンの跡などが白く濁る不良
【想定される原因】 金型の逆勾配、突き出し時の力のかけすぎや傾き
クレージング
放置しておいた成形品の表面に細かなひび割れが出る成形不良
【想定される原因】 禍充填
層状剥離
成形品が層状に重なり、雲母のように剥がれる成形不良
【想定される原因】 成形条件が不適正、混ざり合わないプラスチック混入
お客様お困りの声 (セミナー事前アンケート結果)
今回のアンケートでは「黒点」「白点」「シルバー」などの成形不良で困っている声が非常に多かったです。
- ナチュラル色の成形で黒点が発生することがあります / 自動車部品メーカー様
- 難燃PPをメインに生産しており、異物不良(黒点)改善で苦戦しています。粉取機(サイクロン式)も使用しており、環境異物・加熱筒内の炭化・金型の汚れなどの対策もしておりますが、不良率2%~10%と安定しません / 樹脂製品製造メーカー
- PC材の樹脂部品でシルバー不良が発生します / 電気機器メーカー様
- シルバー不良が根絶できません。また、透明材と黒色材を同じ成形機で生産すると透明材に異物混入が発生してしまいます / 樹脂製品製造メーカー様
- PPS/PBTを多く使用していますが、バージン材に含まれてくる粉が多く困っています / 精密成形部品メーカー様
- シルバー、気泡などの不具合が成形条件の調整で改善しないケースがあります / 電子部品メーカー様
02. 射出成形機メーカーに聞いてみた!粉の問題点とは
- 透明もの白点(異物)は重要と考えるその他は可能性はあるが、透明ものが圧倒的に多い
- 微細な粉はスクリュフライト底部やシリンダ内面に体積してそれらが時々剥がれ落ちて成形品に混入して成形不良をおこすことはある
- 粉はペレットのような表面積がなく微細なため、ヒータからの熱もスクリュー回転による「せん断発熱(ペレット同士がこすり合わさることによる摩擦熱)」も起きないので、固体から溶融状態になる際に、粉のまま混ざってしまうと完全に溶融することなく成形品に充填されてしまうことがある。透明ものでは白濁(天の川模様)が出たりすることがある
- ガラス転移温度の低い樹脂であれば、微細な粉でも溶融できるが、そうでない場合、一般的に粉は微細であるため完全に溶融できず、粉のまま可塑化されてしまうので、そのまま成形品になってしまうことが多いと思う
- 材料の色が黒でコンタミも黒の場合、粉が固化されて固いカーボン状になると、スクリューチップの破損につながる恐れもある
- 粉は溶融できにくいため、それが原因となってシルバーという成形不良もひき超すことがある
03. 実際にお客様で起きた粉による問題点
お客様は日々不良対策に取り組まれており、ハーモのヘリカルホッパーで解決した例も多くあります。
お客様① 電子部品製造メーカー様
- 計量の不安定が発生し、巻き込み・混錬に不具合が発生し、サイクルの不安定が発生する
- また、この現象で可塑化内の均衡性が確保できず、結果的に充填のばらつきが発生し、不良が発生するといったことがネックとなっていた
お客様② 雑貨メーカー様
- 材料搬送時ローダーフィルターが詰まる、掃除の頻度多い
- 吸引力が弱るためサクションホース内ブリッジが起きやすい
- フィルター掃除時、工場内が汚れる
お客様③ 大手電子部品メーカー様
- カーボンニュートラルの課題解決のために、バージン材オンリーから混合材を使うようになった
- しかし、充填不足によるショートが発生するようになった解決策として粉取りタイプのホッパー(ヘリカルホッパー)を使うとショートは全く出なくなった
お客様④ レンズメーカー様
- 成形するにあたり黄変が出てしまい、原因を探ると原料のバージン材が輸送途中の振動により、擦れて出る粉によるものと判明
- 弊社粉取りホッパー(ヘリカルホッパー)を使いながら窒素を注入し、解決した
Q. 粉による計量時間のバラツキはウソ !?
ちなみに、私たちの仮説として持っていた「粉が多いことにより計量時間のバラツキが生じる」というのは、3社の成形機メーカー様から否定されてしまいました…
つまり、混合材などで材料の粒の大きさがが不揃いなことによる計量時間バラツキはあるが、粉が問題で計量時間のバラツキが生じる事はないとのことでした。
しかし! 僭越ながら成形機メーカー様はバージン材に含む粉もしくはリサイクル材25%程度の混合材かと推測します。実際に弊社お客様には粉砕材50%という場合もあり、そうした場合は粉取りをする前と後では明らかに計量時間が短縮された例がありました。したがって、この質問に関しては「粉の量によっては計量時間のバラツキもウソではない…」ということになります。
04. 徹底的に粉塵を除去する「ヘリカルホッパー」のご紹介
粉 発生の原因と影響
- 輸送中に原料袋の中で樹脂同士が接触する
- 樹脂がホッパー等で輸送される時の樹脂同士の接触
- スクリューに付着した炭化物が材料に混ざり込む(黒点の要因)
ヘリカルホッパーの構造・原理
「らせん気流」と「攪拌気流」の二つの気流
- 最初に輸送されてきた樹脂原料をホッパー内で回転させながら、上部のエア吸引口から微粉を捕集します。これが「らせん気流」です
- その後に、ホッパー下部から送られる「攪拌気流」により樹脂原料はホッパー内に再度送りこまれます
- この「らせん気流」と「攪拌気流」の二つの気流によって繰り返しホッパー内を行き来することで、樹脂原料の表面に付着する微粉をさらに徹底して除去します
微粉除去のメカニズムをスローモーションで見る
- 樹脂原料をホッパー内で回転させながら微粉を上部のエア吸引口から回収します
- ホッパー下部から攪拌エアが送風され、微粉の除去を徹底的に繰り返します
- この白い煙のようなものが微粉になります
- 上部に吸引されているのがわかります
- 一方、白い樹脂は上部のフィルターにぶつかって下に落ちているのが分かります
デモ機貸出をご活用ください
ハーモでは『ヘリカルホッパー』のデモ機貸出を無料で行っています。成形不良でお悩みの企業様はお気軽にご相談ください。
05. ヘリカルホッパー導入事例の紹介
導入事例 ①
お困りごと
- 他社製品を使用
- 材料撹拌時に縦方向の気流の力を利用しているため、パンチングフィルターに材料が刺さりやすい
- 目詰まり発生頻度が高く、清掃回数も増えていた
ヘリカルホッパーが解決したこと
- ヘリカルホッパーの材料攪拌時は渦巻き回転のため、材料も刺さりにくい
- 楕円穴のパンチングフィルターを使用することで、ヒゲも取りやすくなった
- 清掃時間の短縮に大きく貢献
複数種類に対応できるフィルター各種
ハーモではさまざまなフィルターをご用意しておりますので、樹脂材料の種類に応じてお選びいただけます。
導入事例 ②
お困りごと
- 半導体工程における粉の問題で困っていた
- 半導体製造のためのガラス基板のケースが、粉による成形不良を起こしていた場合、アウトガスが発生して、ガラス基板そのものにもそれが転移してしまい、ウエハに転写する際のレーザー電光を曇らせてしまう
- ケースの成形製造の前の樹脂材料の段階から粉をほぼ完全に除去して、成形後のアウトガスを発生させないようにする
- ヘリカルホッパーで検証
検証方法
- 目的 ペレットに任意の微粉を混ぜ、ヘリカルホッパーの異物除去効果を確認する
- 材料 導電性樹脂(ペレット)
- 微粉 上記ペレットの材料袋内部にある微粉を使用
- 方法 ヘリカルホッパーで「ペレット単体」「ペレット+微粉」の通過後を確認
検証結果
ヘリカルホッパー通過後の各条件のペレットの状態
他社と比べて樹脂材料に混ざった粉が取り切れているとの評価となり、ハーモのヘリカルホッパーが採用となった。
06. 再生材による成形品質安定に貢献「粒断機」のご紹介
リサイクル材料による成形バラツキを低減する秘密
秘密はハーモ独自の「スイング・プレス・カット方式」
- ハーモの粒断機は通常の粉砕機と違い、樹脂を一定のサイズで連続切断が可能
- 粒もそろって、バージン材に近い形状のため、再生材による成形品質が安定
硬質材粒断例
一定の条件下でPEEKのリサイクルにも対応可能
- 金属代替樹脂と言われるPEEK(ポリエーテルエーテルケトン)は、スーパーエンプラとも言われ、その耐熱性・耐疲労性・耐磨耗性・寸法精度に優れることから、航空機の螺子やナットへの応用が期待されています
- スーパーエンプラと言われる通り、品質性能に優れる反面、未だ樹脂価格は高額で、樹脂特性からリサイクルが難しい樹脂とされていました
- 今般、PEEKのサンプルカットを実施したところ、一定の条件下にてリサイクルが可能であることが検証され、射出成形加工業者様への採用が決定しました。このように技術開発の進歩により、新たな樹脂が開発される昨今、今まではできなかった樹脂のリサイクルにもハーモの粒断機は貢献しています
軟質材粒断例
リサイクルが難しい樹脂もハーモの粒断機でリサイクル率向上!
- PPやPE等のオレフィン系樹脂は、柔らかい特性を持っていることから、リサイクルしにくい樹脂と言われています。粉砕しても引きちぎったような切断となり、ブリッジを頻繁に起こし成形が止まってしまうため、リサイクルを諦めておられる射出成形加工業者様は意外と多い状況です
- また、ウレタン系のエラストマー樹脂やゴム系の樹脂は、汎用の粉砕機ではそもそも切断できない樹脂が多く、射出成形加工業者様から、多くのご相談を頂いております
- ハーモでは、プレス固定刃と移動刃のクリアランスを究極まで狭めることで、ウレタン系・ゴム系の軟質樹脂の切断が可能な軟質系樹脂専用の粒断機を開発。今まではできなかった軟質樹脂のリサイクルを実現いたしました。
成果事例① 自動車部品メーカー様
年間2億円のコスト削減
リサイクル率アップで年間2億円の生産コストを削減!
- ユーザー 某自動車部品メーカー様
- 射出成形樹脂材料 多品種
- 改善結果 ハーモの粒断機を導入し、リサイクル率アップ。年間2億円の生産コストを削減
成果事例② レンズメーカー様
リサイクル率0% → 10%へ
カメラ用レンズの再生材成形品にて「リサイクル率0%」を「リサイクル率10%」にまでアップ
- ユーザー 某カメラメーカー様
- 射出成形樹脂材料 光学系材料
- 改善結果 高級樹脂(3,000円/kg)を使用してレンズを成形していたところ、リサイクル率アップで大幅な生産コスト低減を実現
樹脂リサイクルについてご相談ください
樹脂リサイクルはハーモの周辺機器導入で解決できるかもしれません。私たちハーモにお気軽にご相談ください。
ウェブセミナー資料をダウンロードできます
セミナーの資料をご用意いたしました。成形現場の課題解決にダウンロードしてご活用ください。
ウェブセミナーの動画をご覧いただけます